Ursachen & Lösungen
Fehlerbilder bei Pulverbeschichtungen
Bei Pulverbeschichtungen können verschiedene Mängel auftreten, die nicht nur ästhetisch störend sind, sondern vor allem auch die Qualität und den Nutzen des beschichteten Objekts negativ beeinflussen. Ihnen liegen verschiedene Ursachen zugrunde und sie können während des gesamten Lackierungsprozesses passieren. Sie reichen von Problemen durch eine unzureichende Vorbehandlung der Untergründe über das Auftragen ungleichmäßiger Schichtdicken des Pulverlackes bis hin zu Beschädigungen während des Einbrennprozesses.
Die verschiedenen Herausforderungen bei der Pulverbeschichtung
Bereits eine mangelnde Vorbereitung der Oberfläche des zu lackierenden Objekts kann dazu führen, dass die aufgetragene Lackschicht nicht, unzureichend oder unregelmäßig haften bleibt. Schnell kommt es zudem zu Einschlüssen von Verunreinigungen, die vor allem optisch unschön sind, aber auch zu einer verminderten Schutzfunktion der Beschichtung führen können.
Fehlerpotenzial birgt auch das Auftragen des Pulverlacks. Zu niedrige oder zu hohe Schichtdicken sind nicht ideal. Auch elektrostatische Phänomene können ein negatives Schichtbild besonders bei komplexen Geometrien mit sich bringen. Lackpulver scheidet sich aufgrund einer ungenügenden Erdung oder einer zu hohen Stromstärke beim Auftragen nicht gleichmäßig an Kanten und Ecken eines Substrats ab, haftet partiell nicht auf dem Untergrund oder es entstehen kleine Krater.
Auch während des Brennprozesses muss sauber gearbeitet werden. Zu hohe sowie zu niedrige Temperaturen sind ebenfalls Auslöser für Lackdefekte.
Fehlerbilder im Überblick
Informieren Sie sich vor der Durchführung einer Pulverbeschichtung ausführlich bei FreiLacke. In unserer übersichtlichen Zusammenfassung der typischen Fehlerbilder erfahren Sie nicht nur, welche Ursachen im Detail zugrunde liegen können, sondern auch, wie die ideale Lösung für die einzelnen Probleme bei der Lackierung aussieht.
Pulverspucker
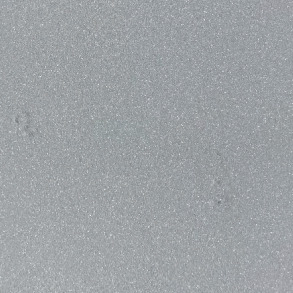
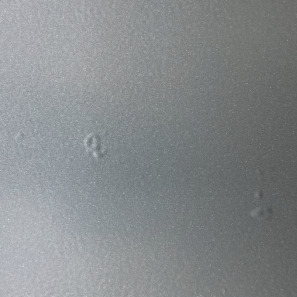
Aussehen
- Pulveranhäufungen auf der Oberfläche
- Nach dem Einbrennofen erscheinen diese als Pulverlackerhöhungen
Ursachen
- Schlechte Fluidisierung
- Verschleiß der Fangdüse
- Ansinterungen im Injektor oder Pulverschlauch
- Feuchtigkeit im Pulverlack
- Feinkörniges Pulver mit schlechter Fluidisierbarkeit
- Eine zu niedrige Luftgeschwindigkeit im Pulverschlauch kann zu Ablagerungen und Pulverspuckern führen.
- Kreislaufbetrieb beeinflusst die Korngröße des Pulverlackes und somit die Fluidisierung.
- Verschmutzungen können ebenfalls Ablagerungen von nachfolgendem Pulver begünstigen und zu unregelmäßigen Pulverausstößen führen.
- Verengungen des Schlauchdurchmessers.
Lösungen
- Fluidisierung prüfen
- Fangdüse prüfen ggf. wechseln
- Kondensationen vermeiden
- Erdung überprüfen
- Pulverausstoßmenge messen
- Überprüfung der Applikationsparameter
- Frischpulver verwenden
- Schlauchverlegung prüfen
- Beachtung der Luftparameter - ggf. Erhöhung der Dosier-/ Zusatzluft. Schläuche mit geringerem Durchmesser oder Radien von mindestens 150–200 mm verwenden.
- Die Pulverrückgewinnung mittels einer Frischpulverzudosierung mit Niveausteuerung aufrüsten.
- Dadurch wird sichergestellt, dass das Verhältnis von Kreislauf- zu Frischpulver stimmt.
- Injektoren und Fangdüsen bei der täglichen Reinigung z.B. mittels Lehre überprüfen und bei Bedarf austauschen.
- Knicke oder Quetschungen, z.B. durch Kabelbinder, vermeiden.
Krater / Benetzungsstörungen
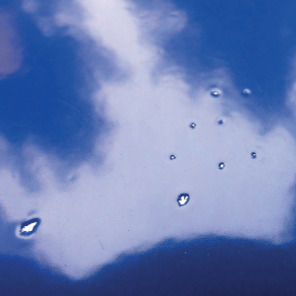
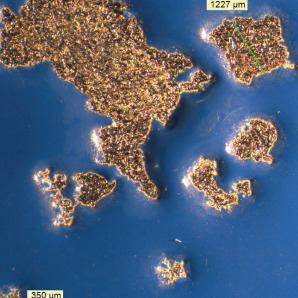
Aussehen
- Meistens kreisrunde Vertiefungen
bis zum Untergrund
Ursachen
- Silikone, Fette, Öle
- Mangelhafte Vorbehandlung (VBH)
- Verunreinigte Umgebungsluft
- Verunreinigtes Pulver
- Feuchtigkeit und / oder Öl in der Druckluftleitung
- Eine mangelhafte VBH reinigt die Substratoberfläche nicht gründlich. Somit verbleiben nicht benetzbare Partikel auf dem Bauteil wie Öle, Fette oder Silikone.
- Verunreinigungen durch nicht miteinander verträgliche Pulverlacke.
- Befindet sich in der Druckluft Öl oder Wasser, kann dies zu Benetzungsstörungen führen.
Lösungen
- Auf Sauberkeit achten
- Überprüfen der Badparameter (VHB)
- Überprüfen der Druckluft
- Pulverlack auf Kontamination prüfen
- Bauteil neu beschichten
- Ständige und regelmäßige Kontrollen der Badparameter in der Vorbehandlung und die entsprechende Dokumentation erhöhen die Reinigungswirkung und Lebensdauer langfristig.
- Eine gründliche Reinigung vor dem Pulverwechsel beugt dem Vermischen verschiedener Pulverlacke vor.
- Überprüfen und warten der Öl- und Wasserabscheider der Druckluft (z.B. mittels Spiegeltest). Wartungspläne zur regelmäßigen Überprüfung erstellen.
Nadelstiche
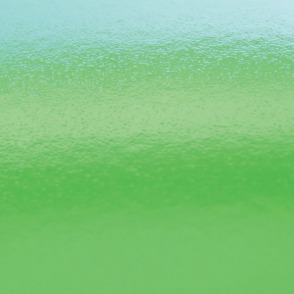
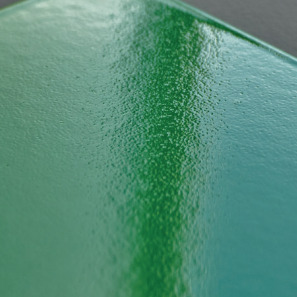
Aussehen
- Microkrater / Poren in der
Beschichtung
Ursachen
- Schichtdicke ungeeignet
- Ausgasungen aus dem Werkstück
- Unverträglichkeit durch andere Pulverlacke
- Sollte die Schichtdicke zu hoch sein, können z.B. Ausgasungen aus dem Substrat oder Abspaltprodukte bei der chemischen Vernetzung nicht durch die Lackschicht entweichen.
- Zu niedrige Schichtdicken könnten eine raue, z.B. gestrahlte, Oberfläche unzureichend abdecken.
- Bei Vermischung von zwei Pulverlacksystemen kann es ebenfalls zu Nadelstichen kommen.
Lösungen
- Schichtdicke optimieren
- Tempern des Werkstückes
- Auf Sauberkeit achten
- Im laufenden Prozess sollte stets die Schichtdicke kontrolliert und nach Herstellervorgabe eingehalten werden. Dies führt nicht nur zur Fehlervermeidung, sondern auch zu einer Kosteneinsparung.
- Unnötig raue Oberflächen, z.B. beim Strahlprozess vermeiden.
- Vor jedem Pulverlackwechsel muss auf Sauberkeit geachtet werden, um eine Verschleppung/Kontamination zu vermeiden.
Stippen (Schmutzeinschlüsse)
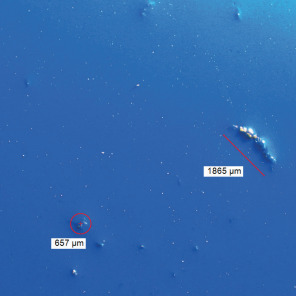
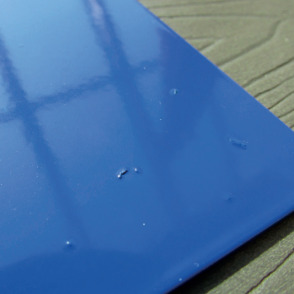
Aussehen
- Einschluss eines Fremdkörpers in der Lackoberfläche
- Untypische Erhebung in der Lackoberfläche
Ursachen
- Verschmutzungen von Anlage, Kabine, Förderer, Ofen
- Farbwechsel
- Werker: Haare, Kleiderfasern etc.
- Fertigungsbedingte Fehlerquellen wie Späne oder Agglomerate
- Werden Kabine, Förderer oder Pulvereinbrennofen nicht regelmäßig gewartet und gereinigt, kann sich Schmutz ansammeln und auf den Bauteilen ablagern.
- Anlagen ohne Siebmaschine sind anfälliger für einen verschmutzen Kreislauf.
- Fertigungsbedingte Pressflöhe oder Pressspäne, die aus der Lackoberfläche herausragen.
Lösungen
- Reinigungsplan erstellen.
- Siebmaschinen reduzieren Verschmutzungen im Pulverkreislauf.
- Regelmäßige Überprüfung der Rohteile führt zu einer Reduzierung der Fehlerrate in den Lackieranlagen.
- Reinigungsplan erstellen.
- Siebmaschinen reduzieren Verschmutzungen im Pulverkreislauf.
- Regelmäßige Überprüfung der Rohteile führt zu einer Reduzierung der Fehlerrate in den Lackieranlagen.
Überbrennen der Lackschicht Versprödung / Vergilbung
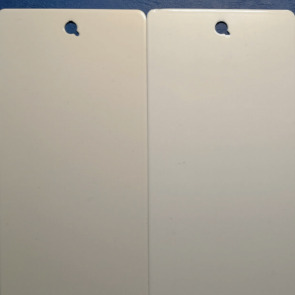
Aussehen
- Je nach Pulvertyp unterschiedlich z.B. Gelbstich bei hellen Pulverlackfarbtönen
Ursachen
- Einbrennbedingungen gem. Herstellervorgaben nicht eingehalten
- In der Regel liegt dies an einer zu langen Verweildauer im Einbrennofen oder an zu hohen Einbrenntemperaturen.
- Durch einen direkt gasbeheizten Ofen kann ebenfalls eine Vergilbung erfolgen
Lösungen
- Ofenparameter überprüfen
- Einbrennbedingungen laut Hersteller prüfen und einhalten
- Verweilzeiten einhalten und bspw. Bandstillstände im Einbrennofen vermeiden
- Einhaltung der Einbrennbedingungen des Pulverlackherstellers.
- Bandstillstände im Einbrennofen müssen vermieden werden. Bei längeren Stillständen muss die Ofentemperatur abgesenkt werden.
- Einsatz eines gasofenstabilisierten Pulverlackes.
Unterbrennen der Lackschicht
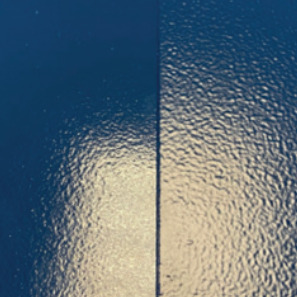
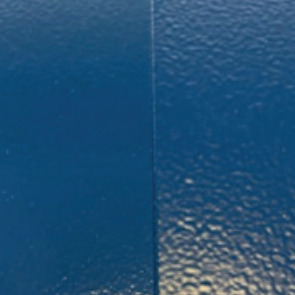
Aussehen
- Zu glänzende Oberfläche
- Schlechte Haftung (Kratzprobe
Ursachen
- Einbrennbedingungen unzureichend
- Durch unzureichende Einbrennbedingungen vernetzt der Pulverlack nicht vollständig. Dadurch können die chemischen und mechanischen Eigenschaften nicht erreicht werden.
- Bei mattierten Pulverlacken kann dies zu einer Glanzerhöhung führen.
Lösungen
- Einbrenntemperatur überprüfen
- Nachvernetzen der Bauteile
- Ofenmessung durchführen
Mittels Ofenmessungen können die Einbrennbedingungen optimiert werden.
Als Faustregel gilt:
Aushärtezeit des Pulverlacksystems (10Min. / 180°C) bei 180°C Umlufttemperatur.
+ 6 Minuten für den ersten mm Objektdicke
+ 3 Minuten für jeden weiteren mm Objektdicke
Mangelhafte Erdung
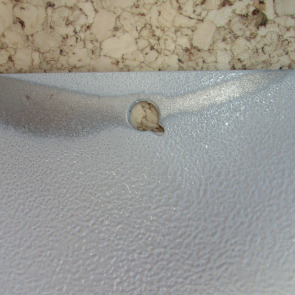
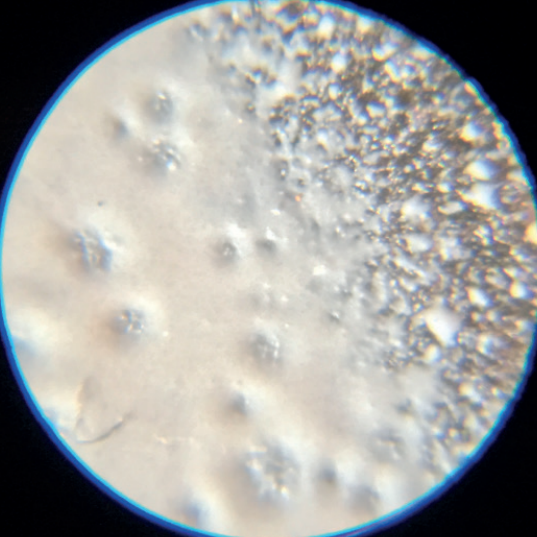
Aussehen
- Pulverlack haftet partiell nicht auf dem Objekt
- Kreisförmige Spannungsdurchschläge
Ursachen
- Elektronen können nicht vollständig abfließen
- Überspannung am Bauteil
- Bei fehlendem Elektronenabfluss kann der Pulverlack nicht am Bauteil haften.
- Oftmals zeigt sich dies durch kreisförmige Spannungsdurchschläge (Rücksprüheffekte).
- Beschichtete Aufhängungen wirken isolierend.
Lösungen
- Erdung überprüfen
- Erdungskabel anbringen
- Unbeschichtete Haken verwenden
- Bauteil sowie Applikation auf Erdung kontrollieren.
- Erdungskabel überprüfen ggf. anbringen.
- Unbeschichtete Aufhängungen verwenden.
- Hochspannung (kV) und Stromstärke (µA) sollten reduziert werden.
Schichtdicke zu niedrig
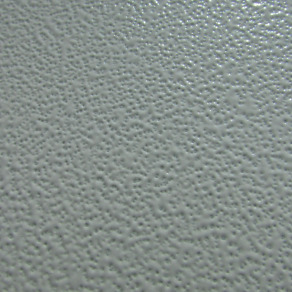
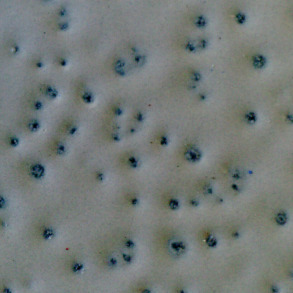
Aussehen
- Durchschimmern des Untergrundes
- Keine geschlossene Pulverlackschicht
- Oberfläche erscheint unruhig
Ursachen
- Pulverausstoß zu niedrig
- Beschichtungsdauer zu kurz
- Pulverlackaufladung nicht optimal
- Entstehung Faraday´scher Käfig
- Erdung mangelhaft
- Zu geringe Pulvermenge (Förderluft).
- Bandgeschwindigkeit zu hoch.
- Verschlissene Fangdüse im Injektor.
- Zu lange Förderschlauchstrecken.
Lösungen
- Applikationsparameter optimieren
- Beschichtungsdauer überprüfen und ggf. erhöhen
- Erdung gewährleisten
- Pulvermenge erhöhen oder Bandgeschwindigkeit reduzieren.
- Durch Optimierung der Hochspannung (kV) und Stromstärke (µA) den Pulverlack gut aufladen.
- Injektor bzw. Fangdüse überprüfen und ggf. erneuern.
- Kurze Förderschlauchstrecken realisieren um optimalen Pulverfluss zu erzielen
Schichtdicke zu hoch
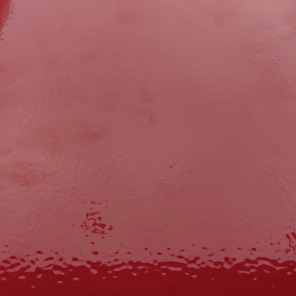
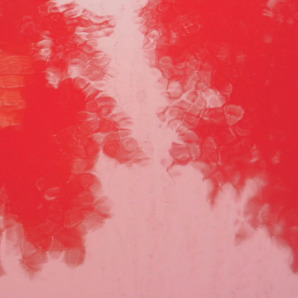
Aussehen
Vor dem Einbrennen:
- Ungleichmäßig
Nach dem Einbrennen:
- Orangenhaut, Nadelstiche
- Fettkanten
- Läuferneigung
Ursachen
- Übermäßige Pulverzufuhr
- Zu hohe Objekttemperaturen beim Beschichten
- Ungünstige Geometrie
- Stromstärke zu hoch
- Relation VBandgeschwindigkeit zu VHubgeschwindigkeit nicht optimal
- Eine ungünstige Bauteilgeometrie fördert einen zu hohen Schichtdickenaufbau.
- Die Sinuskurve der Automatikapplikation überprüfen. Stimmt die Relation von VBandgeschwindigkeit zu VHubgeschwindigkeit nicht, verweilt das Bauteil zu lange vor den Pulverpistolen.
- Bauteile vor der Beschichtung zu heiß.
- Eine zu hohe Stromstärke begünstigt ebenfalls eine hohe Schichtdicke.
Lösungen
- Pistolenparameter optimieren, z.B. Pulvermenge, Spannung, Stromstärke reduzieren
- Abstand Pulverpistole zum Bauteil vergrößern
- Beschichtungsdauer verringern
- Bauteile nicht „heiß“ beschichten
- Vorgetemperte Bauteile länger abkühlen lassen, evtl. mit einem Laserthermometer die Temperatur vor dem Beschichten überprüfen.
- Bei komplizierter Bauteilgeometrie hilft oftmals eine Änderung der Aufhängung.
- Die Sinuskurve der Seitenhubautomaten überprüfen und ggf. optimieren, sodass die Verweildauer der Bauteile und somit die Pulverbeaufschlagung reduziert wird.
Bilderrahmeneffekt
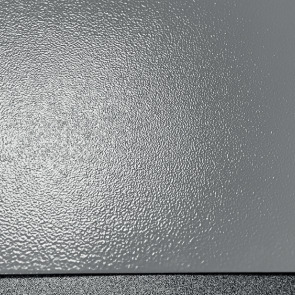
Aussehen
- Oberfläche erscheint ungleichmäßig
- Erhöhte Wulstbildung an Ecken und Kanten
Ursachen
- Stromstärke & Hochspannung zu hoch
- Abstand Pulverpistole zum Bauteil zu groß
- Pulverausstoß zu hoch
- Sind Hochspannung und Stromstärke zu hoch, werden zu viele Elektronen auf das Bauteil befördert. Das elektrische Feld ist an den Kanten am stärksten, deshalb scheidet sich hier eine höhere Pulverlackschicht ab. Dieser Effekt wird zusätzlich verstärkt, wenn die Pistolen zu weit vom Bauteil entfernt sind. Dadurch entsteht ein stärkerer Umgriff. Nach dem Einbrennen zeigt sich dieser als „Bilderrahmen“-Effekt.
Lösungen
- Hochspannung und Stromstärke reduzieren
- Abstand Pulverpistole zu Bauteil verringern
- Geeignete Pistolenaufsätze verwenden (Schlitzdüse, Prallkegel)
- Stromstärke, Hochspannung und Abstand von Pistole zum Bauteil reduzieren. Hierdurch bildet sich eine homogenere Schicht aus.
- Durch Erhöhung der Luftgeschwindigkeit kann der Umgriff ebenfalls reduziert werden
Spannungsrückschläge
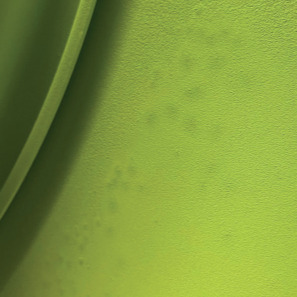
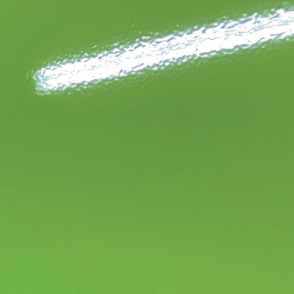
Aussehen
- Erscheinen als Krater mit Verlaufsstörungen auf der Pulverlackoberfläche
- Pulverlackteilchen werden von der Oberfläche abgestoßen („Eisblumeneffekt“)
Ursachen
- Hochspannung (kV), Stromstärke (µA) zu hoch
- Grundierung oder „Erstbeschichtung“ hat eine isolierende Wirkung
- Abstand Pulverpistole zu Bauteil zu gering
- Mangelhafte Erdung
- Spannungsrückschläge sind kleine „Explosionen“ auf der Pulverlackoberfläche. Überschüssige Elektronenanhäufungen, aufgrund zu hoher Hochspannung (kV), Stromstärke (µA), entladen sich hierbei schlagartig.
- Eine Grundierung oder Zweitbeschichtung führt zu einem Lackaufbau mit isolierender Wirkung.
- Ein zu geringer Pistolenabstand zum Bauteil begünstigt dieses Fehlerbild, da sich hierdurch ein stärkeres elektrisches Feld bilden kann.
- Unzureichende Erdung lässt die Elektronen nicht abfließen, dadurch kann es auf der Oberfläche zu Spannungsrückschlägen kommen.
Lösungen
- Hochspannung (kV), Stromstärke (µA) reduzieren und Pistolenabstand zum Bauteil erhöhen
- Erdung optimieren
- Hochspannung (kV) und Stromstärke (µA) sollten reduziert werden.
- Der Abstand zu dem Bauteil sollte erhöht werden.
- Erdung kontrollieren und ggf. optimieren.
- Der Einsatz eines Ionenfängers (z.B. Coronaring) kann hierbei ebenfalls für Abhilfe sorgen.
Faraday´scher Käfig Schlechtes Eindringverhalten in komplexe Geometrien
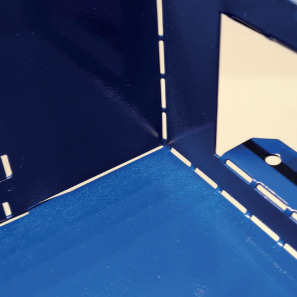
Aussehen
- Ecken, Kanten und Hinterschneidungen werden nur unzureichend beschichtet
- Extreme Schichtdickenunterschiede
Ursachen
- Förder- / Dosierluft zu hoch
- Zu geringer Pulverausstoß
- Keine optimale Düse
- Stromstärke zu hoch
- Mangelnde Erdung
- Abstand Pulverpistole zu Bauteil zu hoch
- Ist die Förder- / Dosierluft zu hoch oder der Abstand Pistole zum Bauteil zu gering, kann das Pulver abgeblasen werden.
- Eine zu hohe Stromstärke / Hochspannung führt in 3-dimensionalen Bauteilen dazu, dass sich der Pulverlack innerhalb dieser Geometrien schlecht abscheiden lässt.
Lösungen
- Förder- / Dosierluft, Stromstärke / Hochspannung oder Pistolenabstand reduzieren
- Triboapplikation anwenden
- Erdung optimieren
- Z.B. Coronaring anbringen
- Pistolenabstand zur Geometrie verringern.
- Förder- / Dosierluft reduzieren (weiche Wolke).
- Stromstärke / Hochspannung reduzieren damit weniger Elektronen aufgebracht werden. Somit reduziert sich der Faraday´scher Käfig und das Pulver kann besser in Ecken und Hinterschneidungen eindringen.
- Reduzierung der überschüssigen Elektronen durch einen Ionenfänger (z.B. Coronaring).
Verunreinigung durch Fremdpulver
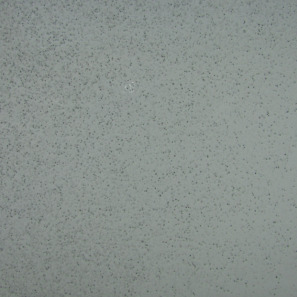
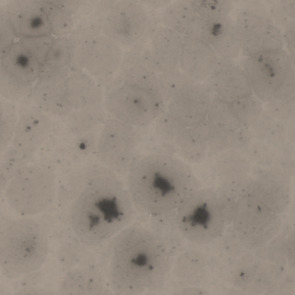
Aussehen
- Andersfarbige Partikel auf der
Lackoberfläche
Ursachen
- Verschmutzter Einbrennofen
- Mangelnde Sauberkeit beim Farbwechsel
- Verschmutzter Förderer / Skid / Laufwagen
- Verschmutzung durch Reinigung
- Ungünstige Luftbewegungen
- Anlagendefekte (z.B. Filter
- Durch ungünstige Luftführungen und zu hohe Luftgeschwindigkeiten im Ofeneinfahrbereich können Pulverpartikel abgeblasen werden, die sich dann auf anderen Bauteilen ablagern.
- Pulverlackpartikel können sich z.B. an der Förderkette ablagern und auf die zu beschichtende Oberfläche fallen.
- Beim Reinigen werden oftmals Pulverlackpartikel aufgewirbelt, welche sich überall ablagern können.
- Liegen Anlagendefekte z.B. am Filter oder Zyklon vor, kann dies zu Verschleppungen / Verunreinigungen im Kreislaufbetrieb führen.
Lösungen
- Pulvereinbrennofen überprüfen und ggf. reinigen
- Höchste Sauberkeit beim Farbwechsel > Kontamination!
- Regelmäßige Reinigung des Förderers bzw. der Laufwagen
- Optimierung der Anlagenreinigung wie z.B. absaugen
- Die Absaugleistung der Pulverkabine überprüfen
- Regelmäßige Überprüfung der Luftführung und Luftgeschwindigkeit im Ofen (Wartungspläne).
- Regelmäßiges Reinigen der Anlagenperipherie.
- Bei der Reinigung der Kabinen sollten im Idealfall Staubsauger anstatt Druckluftpistolen verwendet werden. Dadurch können Verunreinigungen durch Pulverteilchen in der Anlagenperipherie reduziert werden.
Verunreinigung durch Schmierstoffe
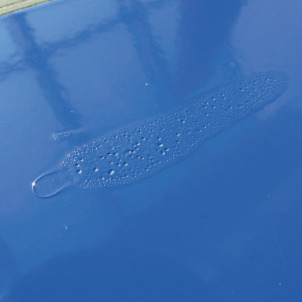
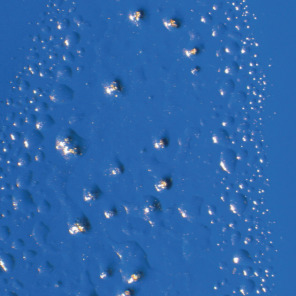
Aussehen
- Kraterähnliche Verlaufsstörungen in
der Lackoberfläche
Ursachen
- Bauteile verunreinigt
- Vorbehandlung ungeeignet
- Öl in der Druckluftleitung
- Verunreinigte Bauteile können Benetzungs- / Verlaufsstörungen hervorrufen.
- Ungeeignete oder defekte Kettenschmierung des Förderers.
- Öl oder Kondenswasser in der Druckluftleitung.
Lösungen
- Geeignete Vorbehandlungschemie verwenden
- Wasser- & Ölabscheider in Druckluftleitung prüfen, ggf. installieren
- Geeignete Vorbehandlungschemie mit VBH- Lieferant ermitteln.
- Regelmäßige Prozesskontrolle der Vorbehandlung.
- Geeignete Schmiermittel für den Förderer verwenden. Kontrolle durch Wartungspläne.
- Öl- / Kondenswasserabscheider prüfen, ggf. ersetzen.
Ausgasungen
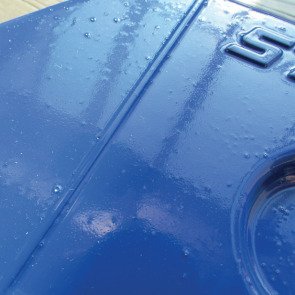
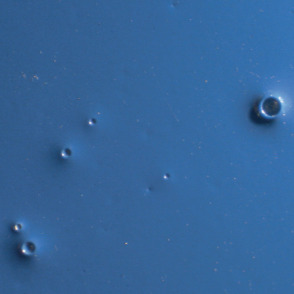
Aussehen
- Nach dem Einbrennen sind
Nadelstiche, Bläschen oder Krater
auf der Oberfläche zu sehen
Ursachen
- Flüssige oder gasförmige Einschlüsse treten bei Erwärmung aus
- Schichtdicke zu hoch
- ungeeignete VBH
- Durch Erwärmung können Gase aus Hohlkammern / Lunker austreten.
- Bei schöpfenden Geometrien können Feuchtigkeitsrückstände Oberflächenstörungen hervorrufen.
- Durch eine ungeeignete Vorbehandlung kann es zu Ablagerungen von Salzkristallen, chemischen Reststoffen oder Ölen / Fetten auf der Oberfläche kommen.
Lösungen
- Bauteile vor der Beschichtung tempern und abkühlen
- Schichtdicke optimieren
- Entgasenden Pulverlack einsetzen
- Tempern der Bauteile kann die Ausgasung vor dem eigentlichen Einbrennvorgang mindern / verhindern.
- Bei wasserschöpfenden Bauteilen kann eine Änderung der Aufhängung Abhilfe schaffen.
- Akklimatisieren der Bauteile kann Kondenswasserbildung auf der Oberfläche verhindern.
- Geeignete Vorbehandlungsmedien verwenden.
- Entgasenden Pulverlack einsetzen.
Schlechte Fluidisierung
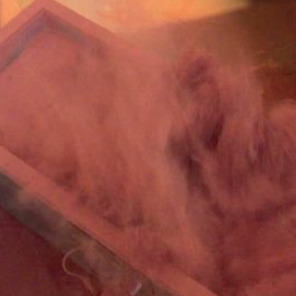
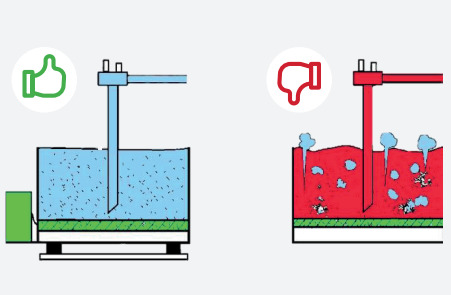
Aussehen
- Fontänenbildung im Fluidbehälter
- Bildung von Luftkanälen im Fluidbehälter
Ursachen
- Fluidluft zu hoch
- Fluidluft zu niedrig
- Unsachgemäße Lagerung des Pulverlacks
- Fluidboden defekt
- Falscher Füllstand
- Zu geringer Füllstand im Vorratsbehälter kann zu inhomogener Fluidisierung führen.
- Im Kreislaufbetrieb kann sich das Kornspektrum des Pulverlacks verfeinern, wodurch es zu Fluidisierungsproblemen kommen kann.
- Ein verstopfter oder defekter Fluidboden hat negativen Einfluss auf die Fluidisierung.
- Öl oder Kondenswasser in der Druckluftleitung, sowie unsachgemäße Transport- / LagerBedingungen können zu Verklumpungen führen.
Lösungen
- Füllstand des Vorratsbehälters prüfen
- Kontinuierlich Frischpulver nachdosieren
- Fluidluft optimieren
- Fluidboden reinigen oder austauschen
- Druckluft auf Feuchtigkeit / Öl überprüfen
- Auf korrekten Füllstand im Vorratsbehälter achten.
- Kontrolle der Niveausonde.
- Kontinuierliche Frischpulver Dosierung im Kreislaufbetrieb.
- Fluidboden regelmäßig reinigen, ggf. austauschen.
- Öl und Kondenswasserabscheider verwenden (Kontrolle durch Spiegeltest).
- Transport- / Lagerbedingungen laut Technischem Datenblatt einhalten.
Bei idealer Fluidisierung „köchelt“ der Pulverlack im Fluidbehälter wie Wasser.
Mit den Experten von FreiLacke Fehlerbilder vermeiden
Bei der Ausbesserung von Fehlern bei Pulverbeschichtungen ist eine genaue Beurteilung des Schadensbildes unerlässlich. Einige Fehlerbilder können so schwerwiegend sein, dass eine vollständige Ausbesserung nicht möglich ist, ohne die Qualität der Beschichtung zu beeinträchtigen. Ein Abtrag der vorhandenen Lackierung und eine komplette Neubeschichtung sind in solchen Fällen der beste Weg.
Umso wichtiger ist es, schon vor dem Beschichtungsprozess auf ideale Bedingungen zu setzen, damit gar nicht erst Lackfehler entstehen. Entscheidend ist dabei unter anderem die Wahl des korrekten Lackes. Auch eine sorgfältige Vorbereitung und Durchführung des Beschichtungsprozesses ist unverzichtbar. Dazu gehören eine gründliche Reinigung der Oberfläche, die Kontrolle der Umgebungsbedingungen wie Temperatur und Luftfeuchtigkeit, die korrekte Anwendung des Beschichtungsmaterials sowie die regelmäßige Wartung und Kalibrierung der verwendeten Beschichtungsanlage.
Entdecken Sie unsere
Lacklösungen
Kosteneffizient, umweltfreundlich und hoch beständig.
Unsere Fokusthemen als Lackhersteller